
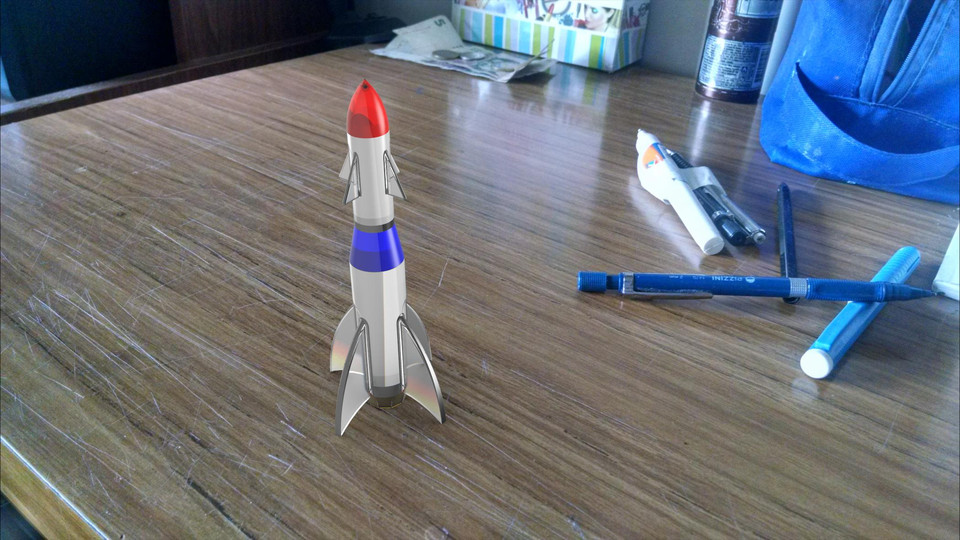
The new models are always generated from scratch. "It's self-optimising, rendering one solution after another, always comparing.
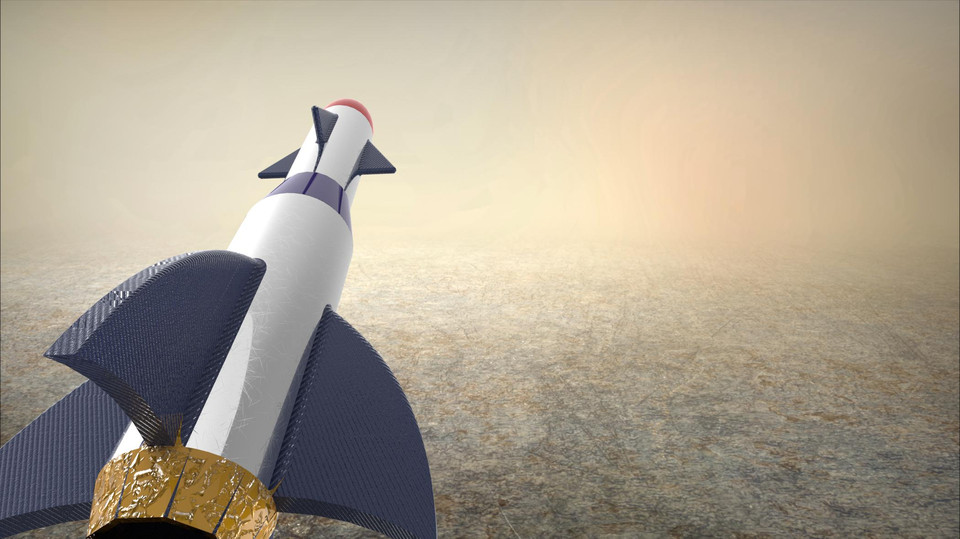
"You test the first design or run simulations of how it would perform, input the data from the test into the algorithm and it uses that to improve the design of the next model," Pham explained. If the process is implemented by an aerospace organisation, the design will be further refined using a digital evolution feedback loop. Hyperganic is currently in talks with different space companies about how this approach could be integrated into their design process. Related story Rise of artificial intelligence means architects are "doomed" says Sebastian Errazuriz "So the inner part is very solid, while towards the outside the structure becomes more porous to save on weight. "We are able to print in different material densities, a method which has not been used in rocket design so far," said Pham. So the process doesn't create a blueprint, but the DNA for an object."įrom there, the information is fed to an industrial 3D printer, which realises it using an aerospace nickel alloy called Inconel 718.
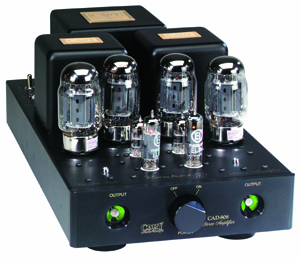
"You're telling the algorithm what you need the object to do and then the algorithm is kind of growing the object with the performance you had in mind, with the specifications. "We compare the process to growing rather than designing," Pham told Dezeen. This algorithm then uses the data to generate the geometry of the final piece from the bottom up. Rather than being translated into CAD files, this information is expressed as formulas and stored in an Excel sheet, in a format that can be read by Hyperganic's algorithm. To create the engine, a rocket scientist first stipulated the core features of a rocket engine – the shape of the combustion chamber and the necessary cooling performance.
